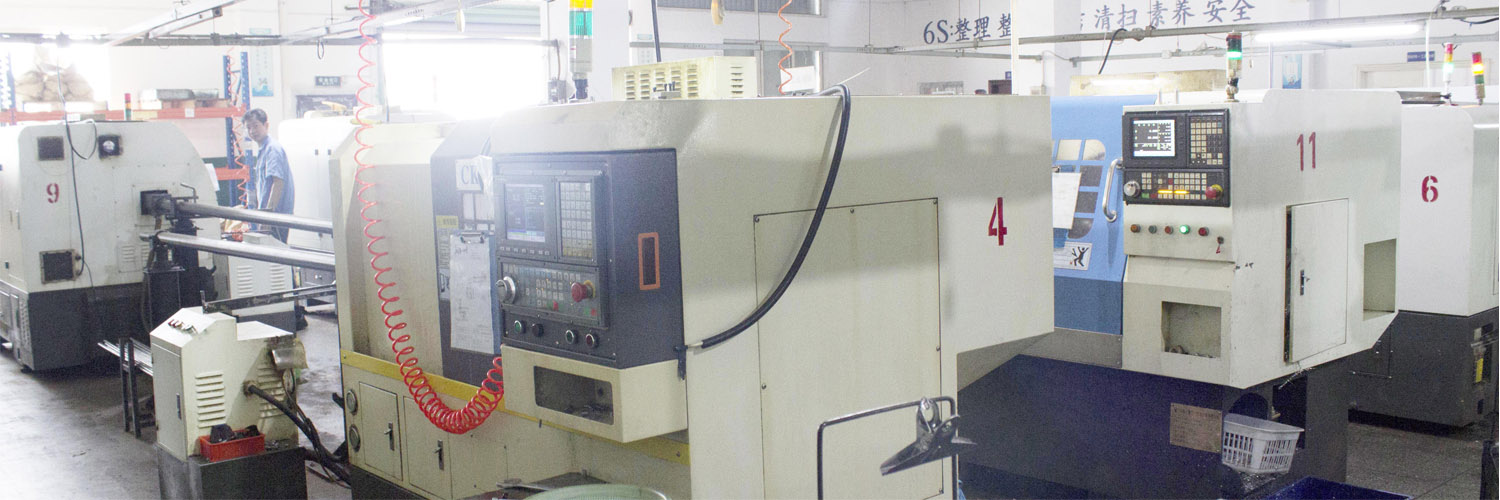
About CNC Machining Parts
As a leading CNC machining manufacturer in China, we deeply focus on customized precision machining of materials such as aluminum alloy, brass copper, stainless steel, etc., and create value for global customers with full process service capabilities. With a professional team that has been deeply involved in the custom parts industry for over 20 years, we are not only able to accurately interpret complex customer needs, but also rely on rich experience and cutting-edge technology to develop one-stop solutions from raw materials to finished products.
Through ISO 9001:2015 international quality system certification, we implement systematic management throughout the entire production process, from raw material inspection to finished product delivery, and implement strict quality control. Relying on a mature global logistics network, we are able to efficiently deliver customized precision parts to various parts of the world, making the precision quality of Chinese manufacturing transcend mountains and seas, and becoming a trusted long-term partner for customers in various industries.
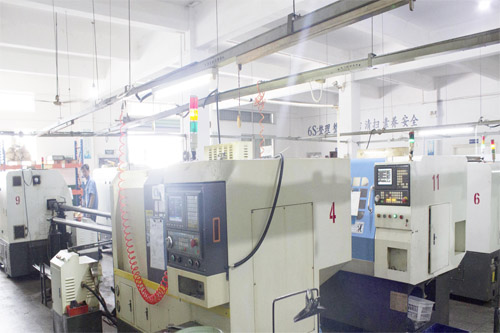
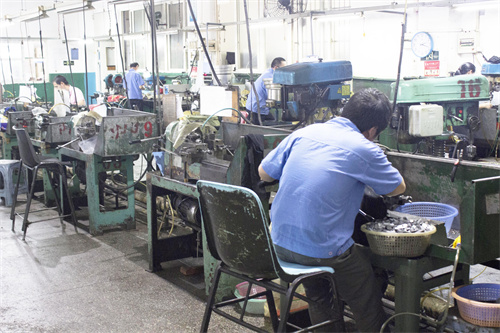
Our Capabilities:
Our more than 50 advanced CNC machines have built a powerful production capacity matrix, with an average monthly processing volume of over 100000 parts. Coupled with a fast turnover mechanism, we can deliver high-quality rapid prototypes in a very short period of time. From high-precision milling and turning to customized machining, we strictly control each process and use three coordinate precision measuring equipment to perform micrometer level inspections on products, ensuring that dimensional accuracy and form and position tolerances meet strict standards, and our error control capabilities are as low as industry-leading levels. Meanwhile, our CNC machining secondary services cover surface treatment, assembly molding, deburring and polishing, further enhancing the functionality and aesthetics of our products.
Application Industries:
Aluminum alloy CNC machining is commonly used in aerospace (reducing aircraft weight), automotive manufacturing (improving fuel economy), electronic equipment (easy to dissipate heat and lightweight), and building decoration fields; Brass and copper CNC machining are widely used in the electrical and electronic (to achieve excellent conductivity), hardware and bathroom (to balance durability and aesthetics), musical instrument manufacturing (to shape high-quality sound), and handicraft industries; Customized CNC machining can meet the personalized needs of multiple industries such as mold manufacturing and medical equipment; Precision CNC machining, with its high precision, is indispensable in fields such as semiconductor manufacturing, optical instruments, and high-end watches that require extremely high precision; Stainless steel CNC machining is commonly used in industries such as food processing (to ensure hygiene and safety), chemical equipment (to resist corrosion), and medical devices (to ensure safety and reliability) due to its excellent corrosion resistance and strength.
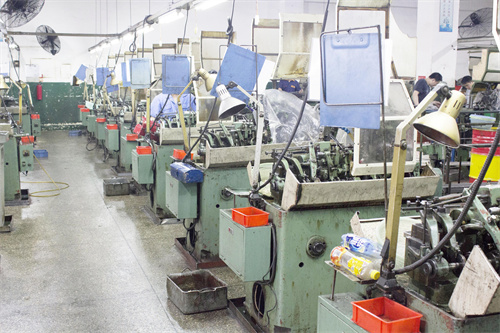
Secondary Processing Services:
We not only provide customized precision CNC machining services for materials such as aluminum alloy, brass copper, stainless steel, etc., but also rely on a comprehensive CNC machining secondary service system to create a one-stop solution for customers from raw materials to finished products. In the secondary processing stage, we use diversified processes to ensure the accuracy and quality of parts according to different materials and application requirements.
For drilling and tapping processes, we use high-precision equipment that can accurately locate on various materials such as aluminum alloy, brass copper, etc., efficiently completing the processing of different specifications of hole diameters and threads to meet various assembly needs; Grinding, grinding, and polishing processes are key means for us to improve the surface quality of parts. Whether it is mirror polishing of stainless steel parts or flat grinding of precision components, the surface roughness can be controlled at an extremely low level through professional equipment and fine operation, significantly improving the aesthetics and functionality of parts.
In the mechanical deburring process, our technicians rely on their rich experience to carefully treat the edges, holes, and other parts of the parts, eliminate residual burrs from processing, and avoid their impact on the assembly and performance of the parts; The parts cleaning process uses various methods such as ultrasonic cleaning and spray cleaning to thoroughly remove impurities such as oil stains and iron filings, providing a clean foundation for subsequent assembly. In the component assembly stage, we strictly follow the design standards, use professional tools and equipment to accurately assemble various parts, and ensure the overall accuracy and reliability of the finished product through multiple testing processes. We provide professional and meticulous secondary processing services to endow each product with higher quality and value.